The hydraulic plate bending machine includes a bracket, a worktable, and a clamping plate. The worktable is placed on the bracket, and the worktable consists of a base and a pressure plate. The base is connected to the clamping plate through a hinge. The base consists of a seat shell, a coil, and a cover plate. The coil is placed in a recess of the seat shell, and the top of the recess is covered with a cover plate. When in use, the coil is energized by a wire, which generates an attractive force on the pressure plate, thereby achieving the clamping of the thin plate between the pressure plate and the base. Due to the use of electromagnetic force clamping, the pressure plate can be made into various workpiece requirements and can also process workpieces with side walls.
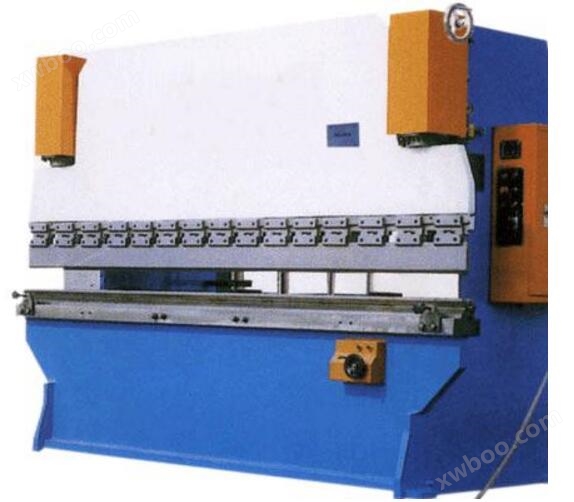
Structure and characteristics:
1. Adopting a fully welded steel structure with sufficient strength and rigidity.
2. Hydraulic transmission, the oil cylinders at both ends of the machine tool are placed on the slider, directly driving the sliding work.
3. The slider synchronization mechanism adopts torsion axis forced synchronization.
4. Adopting a mechanical block structure, stable and reliable.
5. Quick adjustment of slider travel, manual fine-tuning, and counter display.
6. A wedge type deflection compensation mechanism is used to ensure high bending accuracy.
Maintenance and upkeep:
The upper mold should be aligned with the lower mold and then lowered to shut down until the work is completed. If startup or other operations are required, the mode should be selected as manual and safety should be ensured. The maintenance content is as follows:
1. Check the oil level in the hydraulic oil tank every week, and also check it after hydraulic system maintenance. If the oil level is below the oil window, add hydraulic oil; The hydraulic oil used in this machine is ISO HM46 or MOBIL DTE25; The new machine should have its oil changed after 2000 hours of operation, and every 4000-6000 hours of operation thereafter. After each oil change, the oil tank should be cleaned; The system oil temperature should be between 35 ℃ and 60 ℃, and should not exceed 70 ℃. If it is too high, it may cause deterioration and damage to the oil quality and accessories.
2. The filter should be replaced or thoroughly cleaned every time the oil is changed; If the machine tool has related alarms or other filter abnormalities such as poor oil quality, it should be replaced; The air filter on the fuel tank should be inspected and cleaned every 3 months, preferably replaced every year.
3. Clean hydraulic components (substrates, valves, motors, pumps, oil pipes, etc.) monthly to prevent dirt from entering the system and avoid using cleaning agents; After using the new machine for one month, check if there is any deformation at the bends of each oil pipe. If there is any abnormality, it should be replaced. After using it for two months, tighten all the connections of the accessories. When doing this work, turn off the machine and let the system have no pressure.

Debugging and operation:
1. After the hydraulic bending machine is installed and leveled, first wipe off the rust proof oil at each sliding and processing surface of the hydraulic bending machine, and carefully clean it. According to the equipment lubrication diagram, refill the appropriate lubricating oil at each sliding point as required.
2. Check the firm bolts at each connection to prevent loosening caused by transportation and lifting from affecting the use and safety of the hydraulic bending machine.
3. Clean the fuel tank, check the filter screen, and add sufficient hydraulic oil as required. According to the instructions, add hydraulic oil to the return oil of the oil pump.
4. Check the electrical components, ensure there are no safety hazards, connect the power supply, start the motor, confirm the correct direction of the oil pump, and perform a three minute idle run.
5. Select the electrical button to the jog position, step on the foot switch, and allow the hydraulic bending machine to travel up and down several times without load to check if all electrical and hydraulic components are working properly.
6. Trial folding plate: Select a reasonable lower die V-groove and hydraulic bending machine pressure based on the thickness and length of the plate. The trial folding plate should be thin first and then thick, and the pressure should be small first and then large, in order to check the execution of commands by various components.
Selection method:
Based on your own processing dimensions, determine the specifications and models of the hydraulic sheet metal bending machine you want to purchase. In addition, consider the future needs of the enterprise after expanding production scale, and leave a certain margin to determine the specifications and models of the shearing machine. After determining the specifications and models of the hydraulic sheet metal bending machine, you can contact the manufacturer and listen to their opinions. If you think it's good, you can consider it. Confirming which manufacturers produce the hydraulic sheet metal bending machine to purchase is often the easiest aspect for consumers to overlook, because no matter which manufacturer they contact, they will say they specialize in producing this model of hydraulic sheet metal bending machine. In fact, some manufacturers produce very different model numbers, which requires consumers to pay special attention to. Choosing the hydraulic sheet metal bending machine that suits them is the most important thing. After contacting multiple manufacturers of hydraulic sheet metal bending machines and obtaining their prices, parameters, configurations, and payment methods, choosing the manufacturer to purchase is the most important step. Generally, it is recommended to select a reliable manufacturer after removing the lowest and highest prices, in order to obtain a good cost-effectiveness while ensuring the quality and after-sales service of the hydraulic sheet metal bending machine. Choose several special hydraulic sheet metal bending machine manufacturers to compare with each other, and gain a better understanding of the usage of customers who have purchased hydraulic sheet metal bending machines in the surrounding area, the quality and stability of hydraulic sheet metal bending machines, especially the after-sales service of hydraulic sheet metal bending machines. Taking into account various factors, it is advisable to choose a hydraulic sheet metal bending machine manufacturer with the best price and service. It is best to visit and investigate relevant hydraulic sheet metal bending machine manufacturers.
Technical parameters:
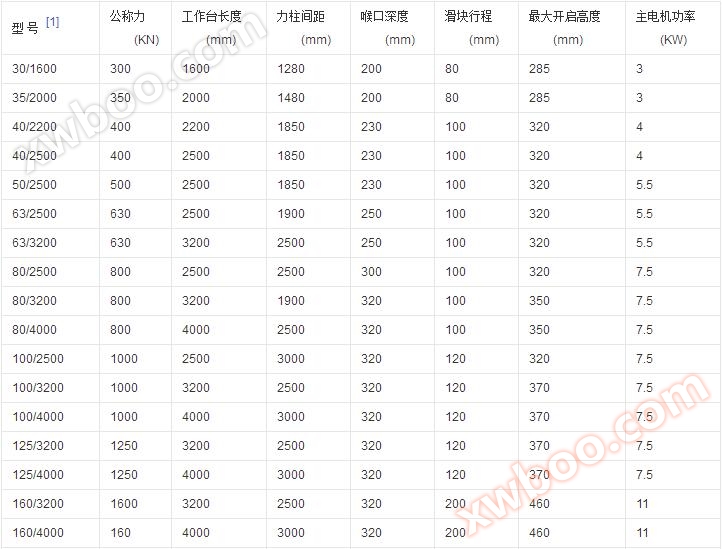